環境活動レポート 2013年度 環境活動レポート
7.当社の製品で環境の改善を行った事例
当社では環境を配慮した商品開発と生産・サービスを行い、お客様の仕様場面での省エネルギー・CO2削減に貢献できるよう活動しています。当社装置での省エネルギー事例や、当社の新しい乾燥システム(オーカワラハイブリッド乾燥システム)について紹介致します。
1)【ヒートポンプを利用したハイブリッド乾燥システム】特許出願中
ハイブリッド乾燥システムは熱風乾燥機の熱風発生部に高効率なヒートポンプ式熱風発生装置(CO2熱風ヒートポンプ)と従来のエアーヒータを最適な条件で組合せることにより、大幅な熱効率向上と省エネルギー化を達成できる全く新しいシステムです。ハイブリッドな加熱システムにより乾燥機に必要な温度の熱風を供給できますので様々な乾燥装置に適用できます。また、チラー水を供給できますので加熱と冷却を同時に行うことでさらに高効率な運転が可能です。この他、熱源として従来は捨てていた常温水、低温の乾燥排ガスなどから熱を汲み上げて乾燥に利用することができます。
事例:既設乾燥設備の熱源をハイブリット化
![]() |
![]() |
上記はお客様の既設乾燥設備熱風発生源にヒートポンプ式熱風発生装置を増設したフローです。
熱風発生源をハイブリット化した結果、二酸化炭素排出量及びコストの削減に成功しました。下記グラフに蒸気使用量、電気使用量の変化を挙げます。
![]() |
![]() |
2)脱臭炉改造及び風量調整によるCO2削減
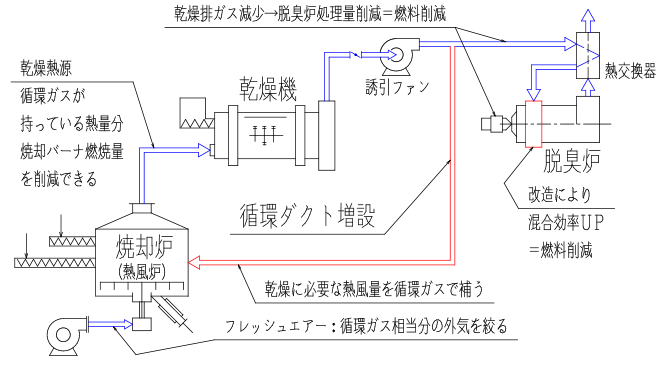
上記フローシートはし尿処理場様へ納入した当社の一般的な乾燥焼却設備を示します。
脱水汚泥の乾燥を目的とした設備で、乾燥汚泥は焼却炉にて焼却、又は外部へ取り出し堆肥化原料となります。焼却炉における乾燥汚泥・残渣、またはバーナの燃焼が乾燥熱源となります。汚泥の乾燥で発生する臭気は、脱臭炉において燃焼脱臭を行った後、排気します。
事例では、既設乾燥設備の脱臭炉内部を改造し、滞留時間・輻射伝熱・混合効率を上げることにより、従来より低い脱臭温度で同等の性能を出せ、脱臭バーナ燃焼量を抑えています。また、乾燥排ガス循環経路を増設することにより、脱臭炉負荷(処理風量)が軽減し、更に脱臭バーナ燃焼量を抑えることができます。乾燥熱源となる焼却炉では、外気(冷風)より熱量を持った循環ガス(乾燥排ガス)を使用するため、焼却バーナ燃焼量を抑えることができます。以上により、乾燥焼却設備全体で、約10~20%のバーナ燃油量削減に成功しています。
導入実績 | 使用燃料 | 改造前燃油量 | 改造後燃油量 | 削減率 | CO2削減量 |
---|---|---|---|---|---|
A社様 | 混合ガス |
- |
バーナ設定変更 ファン:インバータ制御 |
- |
78ton/年 |
B処理場様 脱臭炉改造 |
A重油 |
300kL/年 |
240kL/年 |
20% |
163ton/年 |
C処理場様 循環ダクト増設 |
A重油 |
198.5kL/年 |
177.5kL/年 |
10.6% |
57ton/年 |
D処理場様 熱風炉改造 |
A重油 |
448kL/年 |
378kL/年 |
15.6% |
190ton/年 |
E処理場様 燃料転換 |
灯油+ 都市ガス13A |
灯油2,620kL/年 |
灯油1,080kL/年 13A1,300km3/年 |
- |
936ton/年 |
F社様 フロー改善 |
灯油 |
330kL/年 |
294kL/年 |
10.9% |
90ton/年 |
G処理場様 脱臭炉改造 |
A重油 |
92kL/年 |
80kL/年 |
13% |
33ton/年 |
3)触媒燃焼脱臭
事例1:H社様新規納入乾燥設備
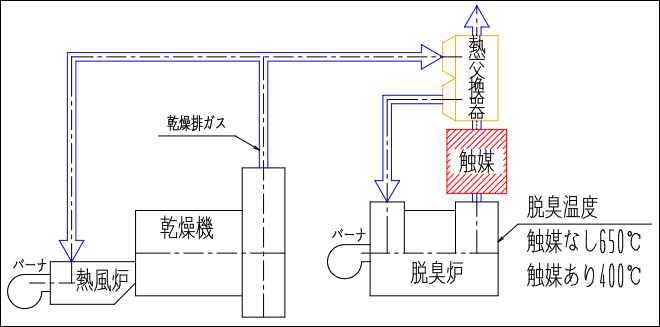
上記フローシートはH社様に納入した乾燥設備を示します。乾燥排ガスには臭気が有り、燃焼脱臭を行った後、排気します。
従来の当社燃焼脱臭炉では650℃以上での運転が必要でしたが、触媒を追加することにより低温(400℃)で排ガス脱臭処理が可能となります。
H社様納入機の場合、脱臭炉において燃料LPGを従来方式で8m3/h使用するところ、5m3/hでの運転が可能となり、年間33tonのCO2削減を実現しています。
事例2:I社様納入既設乾燥設備への脱臭設備増設
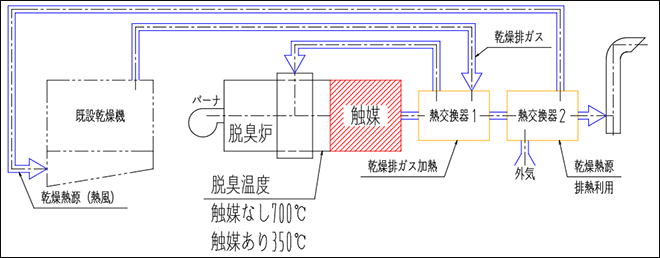
上記フローシートはI社様既設乾燥設備の排ガス臭気対策として当社脱臭設備を納入させて頂いた事例を示します。
従来の当社脱臭炉では650℃以上(700℃)での運転が必要で、I社様納入機の場合A重油を62L/h使用することとなりますが、触媒を追加することにより低温(350℃)での排ガス処理が可能となり、A重油使用量は24L/hで約61%の燃料削減となります。
また、熱交換器1により燃焼脱臭する乾燥排ガスを排熱により予加熱、熱交換器2により排熱を乾燥熱源に利用するなど、徹底した燃費削減に配慮した設備となっています。